The Truth about Prefab: What it Can – and Can’t – Do for Canadian Housing
Canada’s $26B prefab housing bet promises faster, greener builds — but claims of affordability gains don’t hold up under scrutiny.
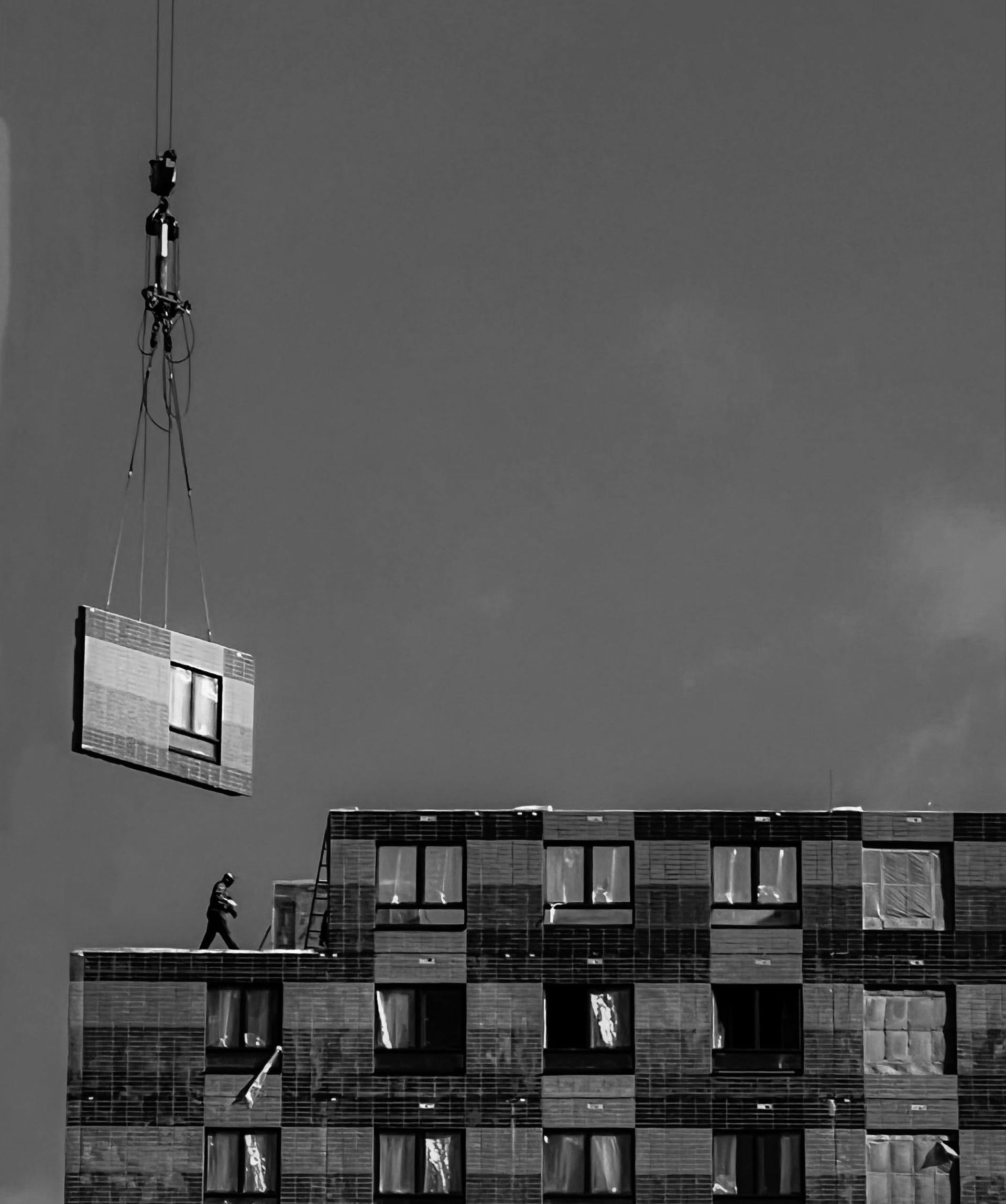
“You may have to fight a battle more than once to win it.”
- Margaret Thatcher
Introduction
Canada has been fighting and losing the housing crisis battle for a decade, and like the Prime Minister before him, Prime Minister Carney vows to change that. In our last two editions of this newsletter, we discussed how likely that is to happen as we’ve reviewed the Build Canada Homes plan and provided critique of what we expect will and won’t work.
However, there is one major aspect of those plans that we have yet to analyze, the government’s bet on pre-fabricated housing.
“BCH (Build Canada Homes) will also catalyze the housing industry and create higher-paying jobs by providing $25 billion in debt financing and $1 billion in equity financing to innovative Canadian prefabricated home builders. Prefabricated and modular housing can reduce construction times by up to 50 per cent, costs by up to 20 per cent, and emissions by up to 22 per cent compared to traditional construction methods” (Liberal Housing Plan).
In this edition of the Bird’s Eye View, we deconstruct this statement, analyzing what we know about recipient eligibility, and the bold claims that pre-fabricated housing can massively reduce construction times and costs.
Recipient Eligibility
In our discussions with industry, it’s become apparent that there is a misunderstanding floating around on who will be eligible for the financing and equity incentive associated with prefabricated housing.
From our reading, this incentive isn’t for the manufacturers of pre-fab panels, mass timber, etc., it’s for the builders who choose to use these solutions.
If the government is going to introduce an incentive, we think this is a smart way of structuring it. Instead of directly subsidizing the manufacturers, the incentive will create demand for pre-fabrication (if this incentive is sufficient to get builders to try it), and introduce builders to new technologies.
Still, whether the incentive makes sense depends on the validity of the government’s claims about the degree to which pre-fabrication can reduce build times and costs, which when it comes to costs at least, we feel are overstated.
Pre-Fabrication Claims
When we read “prefabricated and modular housing can reduce construction times by up to 50 per cent, costs by up to 20 per cent, and emissions by up to 22 per cent”, our hackles immediately go up.
This phraseology sounds an awful lot like the mystical unicorn at the centre of the classic “Good, Fast, and Cheap” Venn Diagram:
Let’s consider what we know about the state of pre-fabrication through the lens of the above Venn Diagram, reviewing each of the claims of Cost, Speed and Quality by appealing to both scientific and anecdotal literature.
Cost
The claims that “prefabricated and modular housing can reduce construction times by up to 50 per cent, costs by up to 20 per cent”, both come directly from a McKinsey & Company whitepaper from 2019. It’s an excellent read, though we have two issues with the government’s use of statistics from it.
First, the authors of that report are largely speaking normatively about what prefabrication ‘should’ be able to achieve as the industry matures, not where the industry currently is. Second, the government omitted stats about the current state.
Let’s take a closer look at the quotes from that paper in their full context.
The authors do state that, “Modular can and should deliver construction cost savings of up to 20 percent - if done right - and can deliver life cycle cost benefits.” (Page 12).
However, only a few sentences later it reads, “But as yet there is no track record of consistent, game-changing cost savings among projects following this model. Indeed, there is often a premium associated with modular construction. This will likely change, however, as the construction industry changes mindset and gains capabilities”.
In short, the authors acknowledge that in the real world, modular construction was often more expensive, not cheaper, and only hypothesized that it would change over time.
There have also been a number of other studies that provide greater clarity.
In “The State of Prefabrication in Canada”, a 2022 market study that is generally bullish on the opportunities for pre-fabrication in Canada, the authors concluded, “Often offsite construction has a higher upfront capital cost and a longer breakeven period which results in little or no construction cost savings. Add in the hard costs of labour, material, and transportation, and offsite construction will be more expensive than conventional projects.”
In fairness, that paper also notes that there are many soft benefits associated with off-site building that do affect the bottom line, but aren’t necessarily captured by comparisons to traditional on-site building. These are mostly benefits that come from shorter project times, including lower financing costs and general contractor costs. There may be earlier revenue from faster completion and also potential savings associated with energy efficiency, which is generally easier to achieve in pre-fab solutions.
In his 488 page
PhD thesis on the subject, Malay Dave conducted a thorough review of available literature, ultimately finding that there are multiple studies showing evidence in both directions. He states, “It is often claimed that prefab costs less or that it is more affordable compared to TOC [traditional onsite construction]. However, the literature review presented earlier suggests that prefab’s role in delivering reduced cost and thus higher affordability may not be straightforward.“
Even where the industry is more developed, such as in China, studies have found that capital costs with pre-fab housing are significantly higher, and that in many instances, labour savings aren’t sufficient to make up the additional capital costs. However, they also note that savings are possible when considering the full lifecycle of the building (Study 1,
Study 2,
Study 3).
Anecdotally, the builders we speak with are finding that at the present time, using pre-fabricated solutions isn’t cheaper, which appears to be consistent with reported experience (Global News,
Storeys).
Our take on Cost:
Currently, it strains credibility to claim that prefabrication can decrease costs by 20%. It’s often more expensive.
Might it one day get there? Sure. But today, pre-fabrication isn’t a cost-saver. The equation may change on a ‘whole life cycle’ cost basis, but that’s an issue for developers that are responsible for higher upfront costs.
Maybe this $26B incentive program will be enough to make up the difference and catalyze the industry towards lower long-term costs, but let's not pretend pre-fab is cheaper today.
Speed
This is likely the least controversial of the three. While there are papers and studies that contradict each other when it comes to price and quality, most research has consistently found that pre-fabricated construction is faster, with the claim of up to 50% being a reasonable upper-bound.
The primary speed advantage comes from being able to manufacture building components while the foundation is being poured on site, but there are also speed advantages from indoor production, less congestion with on-site workers, and design standardization where the same design is being re-used.
Naturally, those projects that are more complex and customized yield less time savings, while those that can be repeated without modification yield the most time savings.
Our take on speed:
Pre-fabrication leads to faster projects, and the 20-50% faster figure used appears reasonable.
Quality
Quality is quite all-encompassing, but for the purposes of this discussion we will only consider the points of energy efficiency, durability/craftsmanship, and aesthetics.
Energy Efficiency
Energy efficiency is one of the strongest arguments for pre-fabrication. While there is variance between pre-fabrication solutions, on the whole, studies consistently and conclusively show lower energy use from pre-fabrication (South Korea,
China,
U.S.).
This is particularly relevant where stringent energy efficiency standards are being implemented across Canada. Back in 2023, we wrote an
article about the BC Energy Step Code, which requires that homes in BC be built to higher energy efficiency over time. In 2025, we are at Step Code level 3, which requires a 20% energy efficiency improvement versus the 2018 building code standards. By 2027, level 4 will be required (40% energy efficiency improvement) and by 2032, level 5 will be required (80% energy efficiency improvement).
From our discussions with builders, step 4 will be very difficult (and increasingly costly) to achieve using traditional building methods and step 5 is nearly cost prohibitive. That said, these levels are readily achievable in pre-fabricated solutions.
It’s entirely possible that increasing energy efficiency standards will be the primary driver behind the shift to pre-fabricated solutions. In BC, that may happen as soon as 2027 when step code level 4 comes into effect and the corresponding costs of building to that standard will increase.
Durability/Craftsmanship
On the issue of durability, there isn’t much reported difference between traditional and off-site builds. The factory construction process helps prevent exposure of materials to the elements and a high level of quality assurance can be maintained at the factory.
As long as sound transportation and crane practices are implemented and skilled onsite finishing teams are used, quality should be comparable and will depend on the team doing the work.
Aesthetics
This is a challenging one. There are loads of examples of beautiful pre-fabricated or modular buildings, but it generally takes a high degree of customization to get it there, which adds to the cost. The greatest savings from pre-fabrication come from standardization and repeatability, so if we are really wanting affordability, cranking out a handful of designs with minimal customization is the lowest cost option.
A cursory review of the Canada Housing Design Catalogue, a federal initiative to provide standardized designs for affordable housing, has us feeling like buildings could all have the same look and feel. The question remains as to whether people will be O.K. with that or not.
Our take on Quality:
We don’t have any concerns when it comes to the quality of pre-fabricated options. It will be easier to achieve higher levels of energy efficiency with pre-fab, which should theoretically add value to a home, but remains to be seen whether it actually does.
While we acknowledge that there are savings to be had in repeatability, we suspect that the industry will eventually land in a happy middle ground for most projects, where some degree of customization and extra features will be added to improve aesthetics, even though it adds to build time and costs.
Conclusion
After reviewing enough studies to make our eyes bleed, we aren’t convinced that pre-fabrication is going to move the needle on affordability the way that the government wants it to, but it does have redeeming features.
The truth is that pre-fabrication isn’t usually cheaper, rather, it’s often more expensive. On the bright side, it’s faster to build, can still be high quality, and offers excellent energy efficiency. Hailing back to the 'Good, Fast, Cheap' diagram, pre-fabricated housing is likely to be good and fast, but not cheap.
We are curious to learn more about the structure of the proposed $1B in equity and $25B in financing for builders that utilize pre-fabricated solutions. It’s wholly possible that these incentives will move the needle on pro-formas enough to see builders move towards pre-fabricated solutions, and this transition will likely be accelerated by ever-increasing energy efficiency standards.
Pre-fab won’t solve affordability, but paired with targeted incentives and rising energy standards, we do feel it will play a meaningful role in reshaping how we build in Canada.
SUBSCRIBE TO THE BIRD'S EYE VIEW
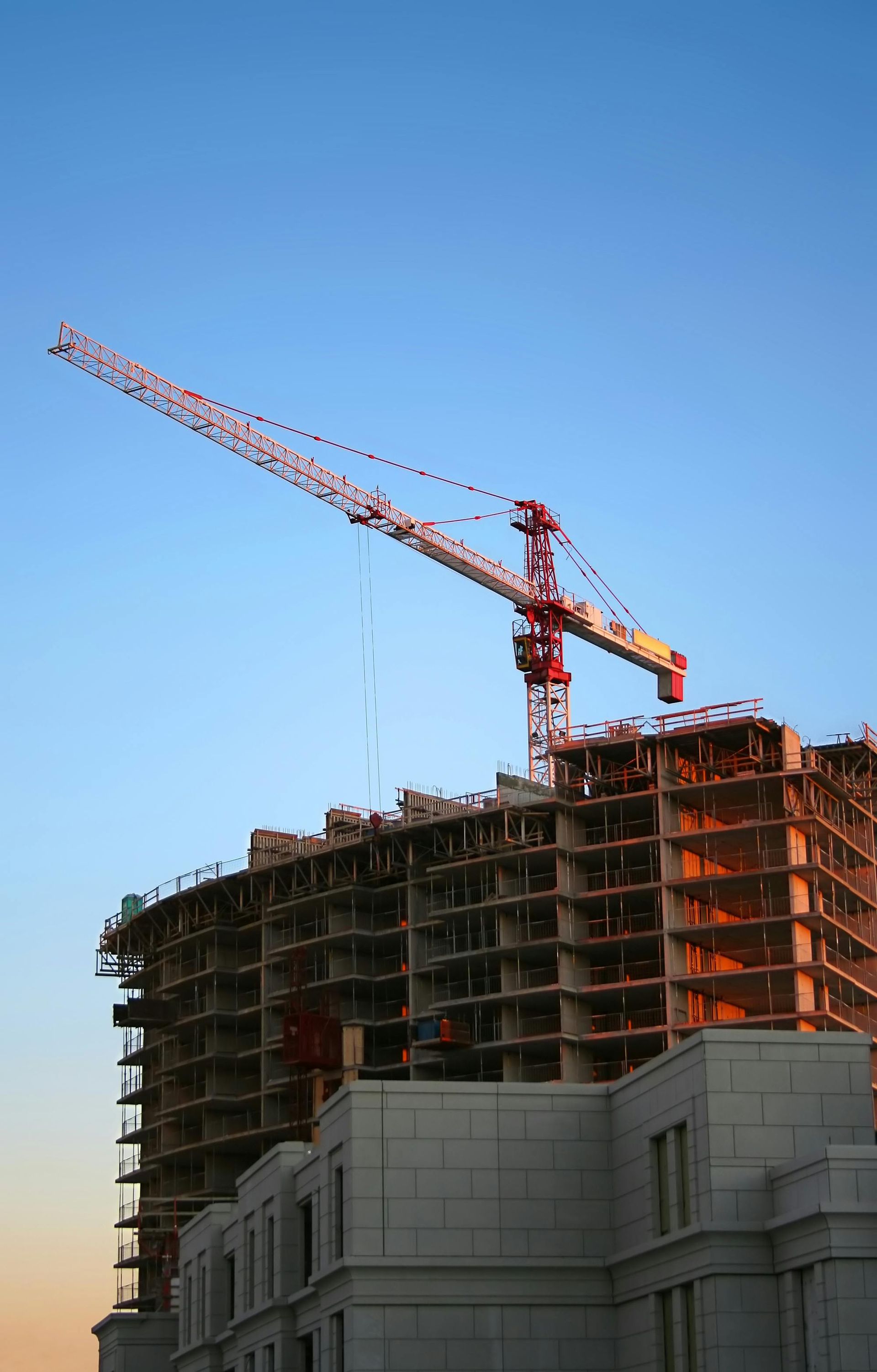
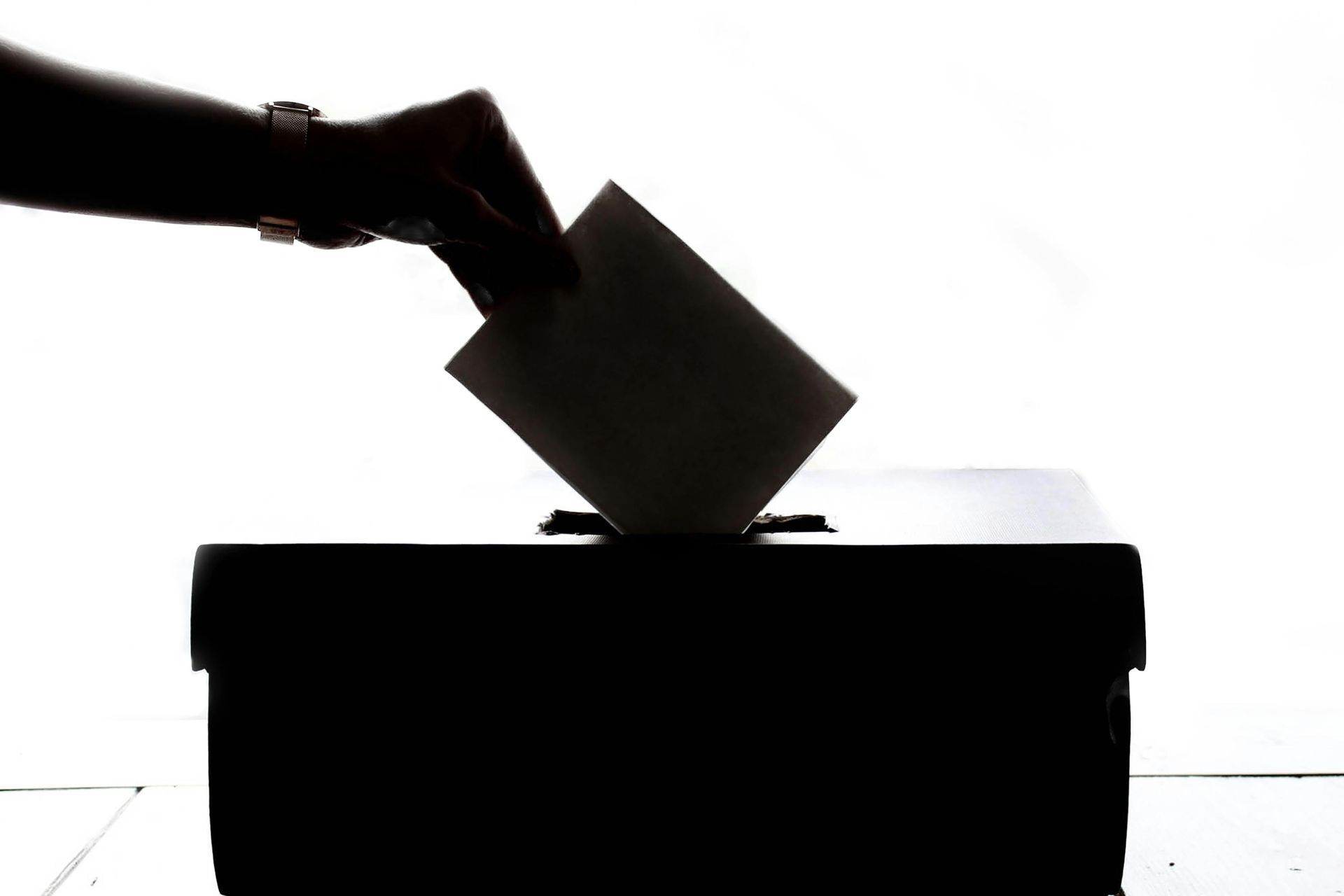